The Rise of Robotics in Warehousing: Impact and Considerations
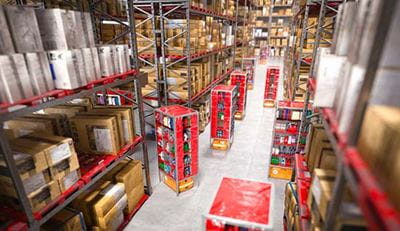
Warehouse robotics adoption is accelerating, driven by labor shortages, AI advances, and operational demands, with nearly 50% of large warehouses expected to deploy robotic systems by the end of 2025. Discover the types of robotics reshaping operations, the efficiency and safety gains they deliver, and practical strategies for successful, cost-effective implementation.
The transformation of warehouse operations through robotics has accelerated at a pace few industry veterans anticipated, even five years ago. The convergence of artificial intelligence, advanced navigation systems, and increasingly affordable autonomous platforms has created unprecedented opportunities for warehouse modernization.
Today's warehouse managers stand at a crossroads: embrace the robotic revolution transforming their industry or risk falling behind competitors who leverage these technologies to achieve remarkable efficiency gains, cost savings, and safety improvements.
The Evolving Landscape of Warehouse Robotics
The numbers tell a compelling story about the rapid adoption of robotics in warehouse environments. By the end of this year (2025), nearly 50% of large-scale warehouse facilities are expected to adopt some form of robotics, with AI-driven solutions becoming increasingly standard. This adoption surge isn't merely a passing trend, but a fundamental shift in how warehousing operations function. The global warehouse robotics market reflects this transition, projected to expand at an impressive compound annual growth rate (CAGR) of 18.2% from 2024 to 2032, potentially reaching $41.7 billion by 2032.
What's driving this remarkable growth? Labor challenges constitute a significant factor. With 37% of companies citing labor shortages as a major supply chain disruptor, robotics offers a viable solution to fill critical operational gaps. The International Federation of Robotics reported a stunning 48% increase in service robot sales in 2022 alone, largely attributed to staffing shortages pushing companies toward automation. Within this broader trend, robots designed for transport and logistics lead the market, with sales growth of 44% and more than 86,000 units sold in 2022.
Types of Robotic Systems Transforming Warehouses
The warehouse robotics ecosystem has evolved beyond simple automated guided vehicles into a diverse array of specialized systems:
Autonomous Mobile Robots (AMRs): Unlike their predecessors that followed fixed paths, modern AMRs navigate independently using sophisticated sensors and AI to determine optimal routes in real-time. This dynamic navigation capability makes them particularly valuable in warehouses with changing layouts or frequent inventory reorganization. AMRs with advanced navigation systems are becoming commonplace in warehouses and logistics for efficient material handling.
Collaborative Robots (Cobots): Designed specifically to work alongside human employees, cobots feature intuitive interfaces and enhanced safety features that detect human presence and adjust actions accordingly. Their ability to learn and adapt to new tasks quickly reduces training time and costs while complementing human workers' skills.
Autonomous Case-handling Mobile Robots (ACRs): These specialized robots excel at handling multiple cases simultaneously. A single ACR can manage up to nine cases at once with total weights reaching 600 lbs, far exceeding what human workers can safely handle. This capability dramatically reduces physical strain while increasing throughput.
Operational Benefits of Robotics Implementation
Warehouse managers considering robotics implementation are understandably focused on the bottom line: will these systems deliver measurable value? The evidence suggests they will. Studies indicate warehouses using robotics experience efficiency increases of approximately 30%. More specifically, facilities implementing robotics witness a 25-30% increase in operational efficiency within their first year of adoption.
These efficiency gains translate directly to productivity improvements. By automating repetitive, time-consuming tasks, robotic systems free human workers to focus on more strategic activities requiring critical thinking and decision-making. This optimal division of labor creates a synergistic effect, with some warehouses reporting productivity increases of up to 50% according to McKinsey & Company research.
The operational benefits extend beyond raw productivity metrics. Automated warehouse robots dramatically improve picking accuracy, reducing costly errors and returns processing. Their consistent performance eliminates variations caused by human fatigue and carelessness, resulting in more predictable throughput rates throughout shifts. Additionally, modern robotic systems collect valuable operational data that can drive continuous improvement across warehouse processes.
Cost Considerations and Return on Investment
While the benefits are compelling, the investment required for robotics implementation varies significantly based on system complexity. Basic systems that improve picking efficiency can cost between $500,000 and $1 million at the low end, while mechanized operating systems can range from $1 million to $5 million or more. More comprehensive solutions, such as semi-automated warehouse conversions, may require $5 million to $15 million, with fully-automated warehouses potentially reaching $25 million.
Determining the appropriate investment level requires careful analysis of several factors:
- The specific warehouse processes requiring automation
- Current operational bottlenecks and inefficiencies
- Anticipated growth in throughput requirements
- Labor availability and costs in your region
- Physical constraints of existing facilities
Rather than viewing robotics as an all-or-nothing proposition, many warehouses benefit from a phased implementation approach that targets high-impact processes first while building institutional knowledge and experience with the technology.
Safety Enhancements Through Robotics
Beyond operational efficiency, robotics offers profound safety benefits, a critical consideration for warehouse managers responsible for both human resources and regulatory compliance. Warehouse robots significantly reduce physical strain and injury risks by handling the most physically demanding tasks. This capability is particularly valuable for repetitive lifting operations and the movement of heavy loads that traditionally lead to musculoskeletal injuries.
Modern warehouse robots come equipped with advanced safety features that prevent collisions and reduce accident risks. Using sensors, cameras, and sophisticated algorithms, these systems can detect obstacles and adjust their routes in real-time, ensuring safe navigation through shared spaces. This capability proves especially valuable in mixed environments where robots operate alongside human workers.
Perhaps most significantly, robotics addresses a fundamental safety challenge: human fatigue. In manually operated warehouses, employees often work long hours performing monotonous tasks under tight deadlines, leading to fatigue-induced errors and injuries. Robots, which don't experience fatigue, maintain consistent performance throughout operations, reducing the likelihood of accidents caused by human error or exhaustion.
Implementation Strategies for Success
Successful robotics implementation requires thoughtful planning beyond simply selecting and purchasing equipment. Integration with existing warehouse management systems, inventory control processes, and physical infrastructure demands careful coordination. The most successful implementations typically involve:
- Comprehensive needs assessment: Identifying specific operational pain points and quantifying potential improvements before selecting technologies.
- Phased implementation approach: Starting with well-defined, high-impact areas before expanding to more complex applications.
- Staff involvement and training: Engaging warehouse personnel early in the process to address concerns, gather operational insights, and develop new skill sets.
- Robust maintenance planning: Establishing preventive maintenance protocols and determining whether in-house expertise or service contracts will best support ongoing operations.
- Data integration strategy: Ensuring robotic systems contribute to broader warehouse intelligence through seamless data sharing.
Warehouse managers must also consider the human dimension of robotics implementation. While 40% of workers initially feel negatively toward automation due to job security concerns, successful implementations emphasize how robotics complements human workers rather than replacing them. The most effective approach positions robots as tools that eliminate monotonous tasks while creating opportunities for workers to develop higher-value skills.
Future Trends Shaping Warehouse Robotics
Looking ahead, several emerging trends will further transform warehouse robotics capabilities. Advanced AI integration will enhance decision-making processes and workflow optimization, enabling robots to understand and respond to increasingly complex situations. These systems will process natural language commands and demonstrate adaptive problem-solving through enhanced machine learning capabilities.
Interoperability between different robotic systems and existing warehouse technologies will become increasingly seamless. Tomorrow's warehouse will likely feature a diverse ecosystem of specialized robots working in concert: AMRs handling transport, cobots assisting with picking, and specialized robots managing packaging and palletizing functions, all coordinated through unified control systems.
Perhaps most significantly, AI and machine learning will transform how robotics function in warehouses, enabling continuous improvement without explicit reprogramming. These self-optimizing systems will identify inefficiencies, adapt to changing inventory patterns, and refine their operations based on accumulated experience.
Partnering for Robotic Implementation Success
Navigating the complex landscape of warehouse robotics requires both technical expertise and operational knowledge—a combination many organizations lack internally. Raymond Handling Consultants offers end-to-end solutions that help warehouse operations "move more, faster, with less cost" through proven intralogistics expertise. With more than 30 years of industry experience, we can provide the equipment, strategic insight, and implementation support needed to maximize efficiency and minimize downtime. Call us for a consultation today.