Preventing Loading Dock Accidents: A Comprehensive Guide
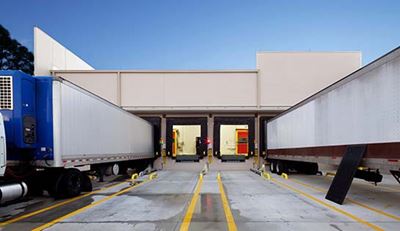
Loading docks are one of the most dangerous areas in warehouse operations, accounting for almost 25% of warehouse accidents. With the right mix of equipment, training, communication, and smart technology, these risks can be dramatically reduced while boosting efficiency and safety culture.
Loading docks represent critical transition points in the supply chain, but they're also hotspots for workplace accidents and injuries. Statistics paint a sobering picture: a staggering 25% of all industrial accidents occur at loading docks. For warehouse managers and supply chain executives, these accidents translate directly to employee injuries, operational disruptions, and significant financial losses. Most loading dock accidents are preventable through systematic approaches combining sound procedures, appropriate equipment, and emerging technologies.
Understanding Common Loading Dock Hazards
Before implementing solutions, we must identify the primary safety threats that exist in loading dock environments. Recognizing these hazards constitutes the first step toward creating effective prevention strategies.
Separation Accidents
Loading dock separation accidents rank among the most dangerous scenarios in warehouse operations. These incidents typically occur when trailers unexpectedly separate from the dock while loading or unloading operations are underway. Four primary types of separation accidents demand particular attention:
Early Departure (Aggressive Pullout): This occurs when truck drivers prematurely leave the dock while forklift operators are still working inside the trailer. A simple miscommunication or assumption that loading is complete can lead to catastrophic consequences when forklifts suddenly lose their support surface.
Trailer Creep: Even properly parked trailers can gradually inch forward during loading operations. The repeated momentum transfer from forklifts entering and exiting creates a dangerous gap between the dock and trailer, potentially causing equipment to tip over or fall between spaces.
Trailer Tip-Over: Structural failures, particularly landing gear collapse on unsecured trailers, can cause the entire trailer to tip forward. This sudden shift endangers anyone inside and typically results in extensive product damage.
Trailer Pop-Up: When weight distribution shifts dramatically during loading operations, the front end of the trailer can suddenly rise, creating an immediate hazard for equipment operators and affecting dock leveler positioning.
Additional Critical Hazards
Beyond separation accidents, loading docks present numerous other safety concerns:
- Fall Hazards: Unprotected dock edges continue to pose serious fall risks for workers.
- Surface Conditions: Wet, oily, damaged, or debris-covered flooring significantly increases slip and trip accidents.
- Forklift Pedestrian Accidents: The combination of busy, congested dock areas and heavy forklift traffic can be a recipe for disaster if forklift operators and pedestrians are not vigilant.
- Atmospheric Hazards: Carbon monoxide from idling trucks can accumulate in poorly ventilated loading areas, leading to serious health complications.
- Unsecured Loads: Improperly stacked or secured cargo can shift unexpectedly during transit or unloading operations.
The Human Element: Training and Communication
While engineering controls and technology solutions play vital roles in accident prevention, human factors remain fundamental to loading dock safety. Comprehensive training and clear communication protocols form the backbone of any effective safety program.
Comprehensive Employee Training
Workers who understand both proper procedures and underlying safety principles make fewer mistakes and respond more effectively to unexpected situations. Training should cover:
- Proper loading and unloading techniques
- Safe forklift operation specific to dock environments
- Forklift pedestrian training
- Recognition of developing hazards
- Emergency response procedures
- Equipment inspection protocols
Remember that one-time training rarely suffices; regular refresher sessions and daily safety reminders help maintain awareness and compliance. Training conducted through multiple modalities, including hands-on practice, written materials, and increasingly, virtual reality simulations, offers the most comprehensive preparation.
Communication Systems
Clear communication between dock workers, forklift operators, and truck drivers prevents many common accidents. Implementing standardized protocols eliminates dangerous assumptions:
- Visual signaling systems (traffic lights, signs, flashing indicators)
- Audible warnings and alarms
- Documented loading/unloading procedures
- Designated communication responsibilities
- Radio or intercom systems for real-time coordination
Many facilities now employ red/green light communication systems that clearly signal when trailer movement is permitted and when loading/unloading operations can safely proceed. These visual indicators eliminate language barriers and reduce miscommunication risks.
Physical Safety Measures and Equipment
The physical infrastructure surrounding your loading docks provides your first line of defense against accidents. Strategic investments in appropriate equipment dramatically reduce incident rates.
Vehicle Restraint Systems
Vehicle restraints represent perhaps the single most important safety device for preventing trailer separation accidents. Modern restraint systems physically secure trailers to the dock during loading and unloading operations. Types include:
- Wheel Chocks: Though basic, properly positioned wheel chocks prevent trailer movement when applied correctly. However, they may not adequately secure trailers in all conditions, particularly on wet or icy surfaces.
- Mechanical Restraints: These systems use hooks or barriers that engage a trailer's ICC bar (rear impact guard), physically preventing forward movement. More sophisticated versions include communication interlocks that prevent dock door operation until restraints are properly engaged.
- Hydraulic Restraints: Offering the highest security level, hydraulic systems provide superior holding strength against trailer movement in any direction.
Dock Equipment Safety Features
Beyond vehicle restraints, several other equipment considerations enhance loading dock safety:
- Dock Levelers: Modern levelers feature toe guards, lip extensions, and automatic return-to-dock functionality that minimize gap hazards.
- Dock Seals and Shelters: Beyond weather protection, these create visual contrast that clearly defines dock edges and trailer openings.
- Safety Barriers and Guardrails: Physical barriers at dock edges prevent accidental falls when doors must remain open without a trailer present.
- Proper Lighting: Adequate illumination both inside trailers and throughout the dock area reduces accidents by improving visibility of hazards and load conditions.
- Dock Plates: These should be properly secured, have adequate capacity for the loads being transported, and feature non-slip surfaces.
Technology Solutions for Enhanced Dock Safety
While traditional safety measures remain essential, technology increasingly offers new dimensions of protection through automation, monitoring, and predictive capabilities.
Automated Warning Systems
Sensor-based systems continually monitor critical safety factors at the loading dock:
- Proximity sensors detect when trailers begin to separate from docks
- Motion detection systems trigger automatic warnings when unexpected movement occurs
- Interlocked restraint systems prevent dock leveler operation until vehicle restraints are properly engaged
- Automated door systems that won't operate until safety protocols are confirmed
These systems remove reliance on perfect human compliance, creating additional safety layers that activate automatically when hazardous conditions develop.
Fleet Management and Optimization
Comprehensive fleet management systems help maintain equipment in optimal condition while ensuring operators receive proper training and certification. These systems track:
- Equipment maintenance schedules and history
- Operator certification status and training needs
- Usage patterns that might indicate unsafe practices
- Collision events and near-misses for follow-up investigation
Through data analysis, these systems help identify both mechanical and operational factors that contribute to accident risks before they result in injuries.
Implementing a Comprehensive Safety Program
Effective loading dock safety requires more than individual solutions, it demands a systematic approach integrating multiple preventive strategies within a comprehensive safety culture.
Risk Assessment and Management
Begin with thorough risk assessment of your specific loading dock operations:
- Identify all potential hazards specific to your facility
- Evaluate the likelihood and potential severity of each hazard
- Prioritize risks based on their potential impact
- Develop targeted intervention strategies for each significant hazard
- Implement regular reassessment as operations change
This methodical approach ensures that safety resources target your most critical risks rather than being distributed ineffectively across minor concerns.
Safety Program Components
A complete loading dock safety program includes multiple integrated elements:
- Documented Procedures: Clear, written protocols for all loading dock operations
- Training Programs: Initial and ongoing education for all workers involved in dock operations
- Equipment Maintenance: Regular inspection and service schedules for all safety equipment
- Environmental Controls: Lighting, ventilation, surface maintenance, and weather adaptation plans
- Emergency Response: Clear procedures for accidents, including first aid and reporting protocols
- Performance Metrics: Tracking of safety indicators, including leading metrics that identify emerging risks
- Regular Audits: Scheduled evaluations of compliance with safety procedures and protocols
Creating a Safety Culture
Perhaps most importantly, effective safety programs require cultural commitment throughout the organization. This means:
- Visible management support and participation in safety initiatives
- Employee involvement in safety planning and implementation
- Recognition and reward for safety compliance and improvement
- Zero tolerance for safety shortcuts, even when they might increase short-term productivity
- Open communication about incidents, near-misses, and safety concerns without blame
- Continuous improvement through regular review and adaptation of safety measures
When safety becomes ingrained in organizational culture rather than merely enforced through rules, compliance rates increase dramatically and accident rates decline correspondingly.
Investing in Loading Dock Safety
The loading dock presents unique challenges in warehouse operations, combining vehicle movement, heavy equipment operation, and manual material handling in a confined, high-activity environment. By addressing each aspect of loading dock safety—from physical infrastructure and restraint systems to training, communication, and emerging technologies—warehouse managers can dramatically reduce accident rates while simultaneously improving operational efficiency.
For organizations seeking to enhance their loading dock safety, Raymond Handling Consultants offers comprehensive evaluation and implementation services. With more than 30 years of experience helping customers move more product faster and with less cost, our team provides the equipment, strategic insight, and proven intralogistics solutions to optimize your efficiency while minimizing safety risks. Don't wait for an accident to highlight vulnerabilities in your loading dock operations! Give us a call today.