Reducing Forklift Accidents with iWarehouse Safety Features
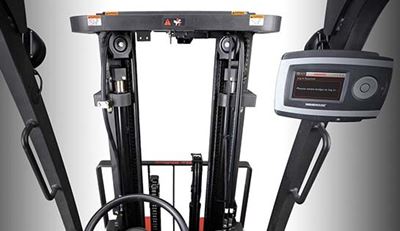
In today’s high-pressure warehouse environments, Raymond’s iWarehouse suite combines advanced access control, impact management, proximity detection, electronic checklists, operator training, and data analytics to proactively prevent forklift accidents while simultaneously improving productivity.
In today's fast-paced warehouse environments, the intersection of productivity and safety remains a constant challenge for operations managers. With forklifts accounting for nearly 100,000 injuries annually in U.S. warehouses alone, finding effective solutions to reduce accidents while maintaining operational efficiency has become a critical priority.
The Raymond iWarehouse suite of technologies offer comprehensive safety features specifically designed to address these challenges through intelligent data collection, real-time monitoring, and preventative controls. These innovations are transforming how facilities approach forklift safety, moving beyond reactive measures to proactive accident prevention systems that simultaneously boost productivity.
Access Control: The First Line of Defense
Unauthorized or inadequately trained operators represent one of the most significant safety risks in warehouse environments. iWarehouse tackles this fundamental challenge through sophisticated access control mechanisms that serve as a crucial first line of defense against accidents.
Operator log-ins help ensure that only authorized and certified users have access to specified vehicles for greater asset and operational security. This system allows managers to remotely manage forklift operator certifications and restrict access to only those properly qualified to operate specific equipment. The technology enforces compliance by requiring operators to verify their credentials before equipment activation, effectively eliminating the possibility of unauthorized usage.
Beyond simple access control, this system allows for remarkably detailed customization of vehicle parameters. Managers can remotely adjust settings such as travel speed and acceleration on a per-vehicle or per-operator basis. This capability proves particularly valuable when managing operators with varying experience levels or when addressing specific safety concerns in specific warehouse zones. For instance, newer operators can be assigned reduced speed limits until they demonstrate proficiency, while all vehicles can have mandated speed reductions in high-traffic or hazardous areas.
Impact Management: Detecting and Preventing Collisions
Even with properly trained operators, collisions remain a significant concern in busy warehouse environments. iWarehouse's comprehensive impact management system addresses this challenge through immediate detection, notification, and long-term analysis of impact events.
The system employs sophisticated forklift impact sensors that provide instant notifications when collisions occur, including critical details about the nature and severity of the impact. These notifications allow management to respond immediately to potential injuries or damage, but more importantly, they create accountability among operators. When operators know their driving behaviors are being monitored and recorded, they naturally adopt more cautious approaches to vehicle operation.
The true power of impact management lies in its analytical capabilities. Managers can compare and contrast impact data for days, weeks, months or years to identify trends and areas of concern, and to facilitate preventive measures—from operator training to warehouse layout changes—to alleviate the problem. This data-driven approach transforms each incident into an opportunity for systemic improvement, addressing not just symptoms but root causes of safety issues.
Proximity Detection: Preventing Accidents Before They Happen
Perhaps the most advanced safety feature in the iWarehouse ecosystem is its proximity detection technology, which works proactively to prevent accidents before they occur.
The iWAREHOUSE FieldSense system represents a significant leap forward in warehouse safety technology. This robust proximity notification system is designed to alert pedestrians and lift truck operators when they come within a predefined distance of properly equipped trucks and pedestrians. By creating awareness of potential collision situations before they become dangerous, the system gives both operators and pedestrians critical extra seconds to avoid accidents.
For facilities with very narrow aisles, the In-Aisle Detection System provides an additional layer of protection. This technology automatically displays 'sensor stop' on the truck display, sounds an audible alarm, and decelerates a truck to a complete stop whenever it detects certain objects in its path. By removing human reaction time from the equation, the system can prevent collisions even in situations where the operator might not notice an obstruction until it's too late.
Electronic Checklists: Ensuring Equipment Safety
Equipment failures represent another significant source of forklift accidents. iWarehouse addresses this through electronic pre-shift checklists that ensure regular inspection of critical safety components.
The system allows for customized forklift checklist questions, including conditional questions, to suit the specific needs of your business. Completed checklists are stored electronically, creating a documented "paper trail" that satisfies OSHA regulatory requirements while eliminating physical paperwork.
More importantly, these electronic checklists enable managers to view the results of pre-operation checklists by operator or vehicle and drill down into details of checklist completions and results including the question and answer that resulted in a failed checklist. This visibility allows for immediate identification of potential equipment issues before they lead to accidents, and also highlights patterns of neglect or oversight that might require additional operator training.
Operator Training and Development
Speaking of training, iWarehouse recognizes that technology alone cannot prevent all accidents—human skill development remains essential. That's why the system includes robust tools for operator training and development.
The Virtual Reality Simulator represents Raymond's cutting-edge approach to operator learning. This immersive tool helps develop more confident, efficient forklift operators by providing realistic training scenarios without the risks associated with training on actual equipment. The simulator can recreate challenging warehouse situations, allowing operators to develop skills and responses in a safe environment before facing those challenges in the real world.
The system also supports ongoing development through data-driven coaching. By utilizing iWAREHOUSE data to identify areas of concern and opportunities for improvement, managers can implement targeted training programs that address specific weaknesses identified by the system. This personalized approach proves far more effective than generic safety training.
Data Analytics: Turning Information into Safety Improvements
The true power of iWarehouse lies not just in its individual safety features, but in its comprehensive data collection and analysis capabilities that transform raw information into actionable safety improvements.
Through the iWAREHOUSE GATEWAY web portal, fleet metrics, lift truck data, key productivity indicators and driver utilization data are all readily accessible from any smartphone, tablet or computer. This intuitive interface allows managers to quickly identify areas of concern and customize views based on location or area of responsibility.
The system's analytical power enables facilities to track everything from individual operator behaviors to facility-wide trends, helping identify potential safety issues before they result in accidents. For example, repeated minor impacts in a specific area might indicate a problematic warehouse layout that needs adjustment, while patterns of checklist failures could highlight equipment maintenance issues requiring attention.
Implementing a Comprehensive Safety Approach
The most effective safety programs integrate multiple approaches, and iWarehouse is designed specifically to support this comprehensive strategy. By combining access control, impact management, proximity detection, electronic checklists, operator training, and data analytics, facilities can address safety from every angle.
This integrated approach recognizes that forklift accidents rarely have single causes. Most incidents result from a combination of factors—perhaps an inadequately trained operator, combined with a blind corner in the warehouse layout, exacerbated by a minor equipment issue. By addressing all these potential factors simultaneously, iWarehouse helps create multiple layers of protection against accidents.
The Bottom Line: Safety and Productivity
What makes iWarehouse particularly valuable is that its safety features don't come at the expense of productivity. In fact, many of the same technologies that improve safety also enhance operational efficiency. Better-trained operators work more efficiently, properly maintained equipment experiences less downtime, and optimized warehouse layouts improve both safety and workflow.
Taking the Next Step Toward a Safer Warehouse
If you're ready to transform your approach to warehouse safety, the Raymond Handling Consultants team offers the equipment, parts, and strategic insight to help you find your peak efficiency, minimize downtime and get more out of your people and equipment. Our experienced consultants can guide you through the process of selecting and implementing the iWarehouse safety features that will provide the greatest benefit for your specific operation. Contact us today to begin your journey toward a safer, more efficient warehouse environment.